Welcome to our
NEW Virtual Showroom
Step into a world of innovation.
Vertical Lift Module (VLM) Enclosed shelf-based storage system designed to increase capacity in a more compact footprint.
Discover nowFully integrated AutoStore™ solutions Take your order fulfillment to the next level
Discover nowIntuitive Picking Assistant (IPA) Maximize productivity and picking accuracy for AutoStore™ Solutions
Discover nowOptimize warehouse space Implement automation to increase storage capacity and minimize footprint.
Discover nowSolutions by industry segment
How do you store your goods?
Kardex Mlog secures continuous replenishment in production of BASF
Kardex Mlog has built two structurally identical, automated buffer storage plants for the BASF chemicals company. The new facility includes warehouse management and conveying technology to connect goods receipt and production.
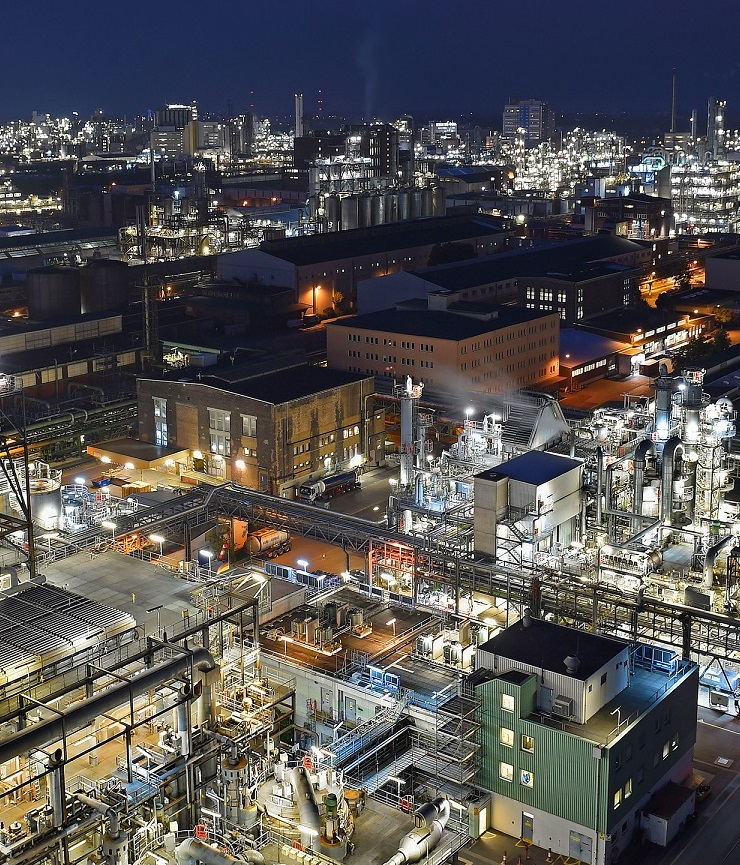